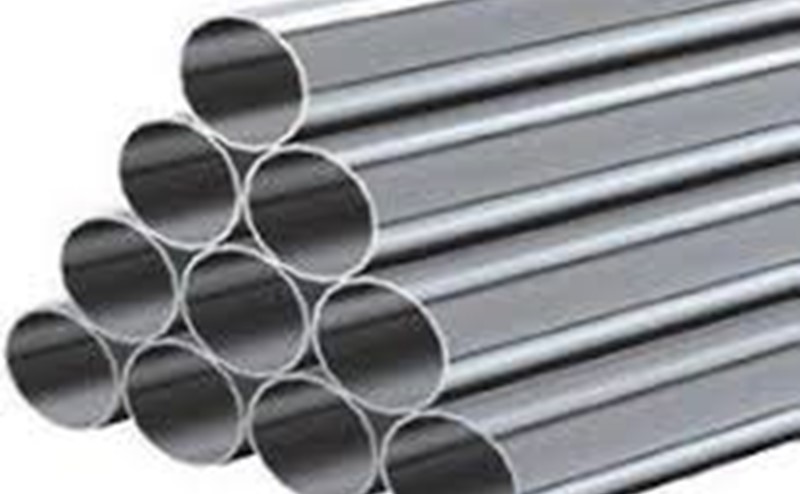
Testing your metal
Specifiers of HVAC systems are presented with a myriad of choices when having to select the best material for use in pipework and other components. There is no 'best' overall solution with the decision on which material to use being dictated by a number of factors such as cost, ease of installation and resistance to corrosion damage. All metals are vulnerable to corrosion under adverse conditions, but the risk can be significantly reduced by correct water treatment and careful operation and maintenance.
What’s important in closed circuit systems in particular, is that oxygen is kept out of this pipework. It is the main driving force for corrosion – either directly, or by creating the right conditions for bacteria to grow. Chemical inhibitors that passivate metal surfaces and control pH also play an important part.
Which material?
Carbon steel: Thin-walled carbon steel has grown in popularity over the last few years due to the fact it is light weight, cost-effective and easy to install.
While an excellent material for pipework, particularly in closed circuit systems, thin walled carbon steel is very susceptible to damage, which can put specifiers and M&E contractors off.
To make the most of carbon steel, it’s essential that care is taken in its transport and storage – it must be kept clean and dry. Once installed, remote corrosion monitoring technology can play an important part in preventing corrosion during pre-commission cleaning (PCC) and ongoing operation. By continuously tracking the level of dissolved oxygen, as well as the root cause of aeration, any changes in condition can be instantly identified and controlled, dramatically reducing corrosion risk and making thin-walled carbon steel a far 'safer' choice.
Chemical inhibitors are also commonly used alongside carbon steel to mitigate corrosion – Hevasure therefore tracks water conditions using conductivity and pH sensors, ensuring they remain at their optimum.
Mild steel: Thicker walled steel is commonly used in older systems and for pipework and other HVAC components, such as pumps.
While mild steel is susceptible to corrosion in the same way as thin-walled carbon steel, wall penetration is less of an issue due to its thickness. Corrosion debris, however, is a problem as it can be transferred round the system causing blockages and loss of efficiency.
When corrosion debris settles in can lead to corrosion in the horizontal section of the pipework and areas of low flow rate, leading to localized pitting attack or creating the perfect location for bacteria to colonise.
Copper: Commonly used in domestic plumbing, but not so much in commercial systems. Copper can be subject to pitting attack if a coherent protective patina fails to form due to adverse water conditions (e.g. presence of ammonia) and dissolved oxygen stays in a system for too long It is also prone to erosion corrosion if water velocities are too high and can also suffer from microbial influenced corrosion (MIC) if bacteria are allowed to settle of surfaces (i.e. become sessile).
Brass: Used for components such as valves and other fittings, brass can be subject to pitting attack if dissolved oxygen stays in the system for too long and or optimum water chemistries are not maintained. Brass can also be prone to erosion corrosion and stress corrosion cracking.
Aluminium: Mainly used in heat exchangers, under the correct water conditions aluminium is passivated and resistant to corrosion. Passivation however is lost if the pH increases above 8.5, resulting in corrosion in oxygenated waters.
Stainless steel: Used in boilers and pipework (especially in process industries), stainless steel is normally passivated but will undergo pitting attack in certain waters or stress corrosion cracking (e.g. chlorinated). Stainless steel boilers are very expensive so must be protected.
Plastics: Plastic is not a metal and therefore not subject to corrosion. It can be a source of aeration, however, if non-barrier plastic pipework is used. Hevasure’s remote monitoring systems have been deployed to check whether the plastic pipework is responsible for high dissolved oxygen levels. Whatever the metal, in closed circuit systems, Hevasure’s 24/7 remote monitoring technology can protect pipework and associated components from corrosion, alerting FMs and maintenance teams of the changes in condition which can lead to serious damage.
By nipping issues such as oxygen ingress in the bud, and keeping track of corrosion rates and crevice corrosion, this costly scourge can be effectively eliminated.
Have the confidence to specify the right pipework for your HVAC systems. Install Hevasure remote monitoring technology.