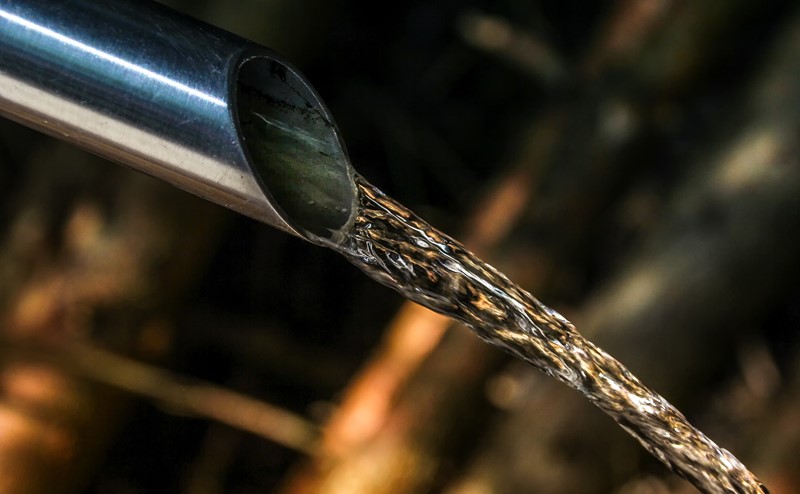
Closed loop HVAC systems explained – FAQs
Keeping closed loop heating systems corrosion free
Water-based HVAC systems transfer heat energy around a building by pumping water through pipework and associated components. Systems are either open to the air – in the case of cooling towers, or closed - in the case of sealed and pressurised designs. Closed loop systems are commonly used for a wide range of commercial HVAC systems, found in office blocks, data centres, schools, hospitals and industrial sites.
What is a closed-loop HVAC system?
Closed-loop systems – sometimes called closed circuit water systems or closed heating and cooling systems - are a key contributor to the overall efficiency of associated HVAC.
As the name suggests, closed-loop HVAC systems are sealed units containing a fixed volume of water. This recirculates under pressure within the system to provide heating and cooling; for temperature control or to absorb excess heat from industrial processes.
Examples of closed loop HVAC systems include:
- Low temperature hot water (LTHW) heating systems
- Heat pumps
- Chilled water systems
- Condenser water circuits
- District heating schemes
If these vital parts of the building services jigsaw puzzle are poorly constructed and maintained they can be vulnerable to corrosion, fouling and scale, wreaking havoc on overall building performance, impacting energy efficiency, creating maintenance headaches and increasing the risk of expensive repairs and breakdown.
Closed-loop heating and cooling – what can go wrong?
In theory, the water circulating within closed loop HVAC systems should be protected from outside contamination. Poor maintenance practices and water treatment can lead to oxygen ingress, however – the precursor to all corrosion issues in closed-loop systems.
If mistakes are made at the construction and pre-commission phases, or systems are not looked after properly, responsible parties could find themselves faced with a system suffering from corrosion, caused directly by oxygen, or where this oxygen has created the right conditions for bacteria to thrive.
While bacteria poses little threat to humans in a closed circuit (legionella is the well-documented health risk associated with open circuits), it can contribute to system fouling and microbial influenced corrosion if left to proliferate.
How can corrosion be prevented in closed-loop systems?
Traditionally, corrosion has been monitored in closed-loop systems using periodic water sampling to determine if remedial action is required. It is now appreciated by many in the industry that this snap-shot view has many short-comings, as often flags up issues too late, and doesn’t detect the root-cause of any problems. Sampling for bacteria can also be misleading as it is only when colonies stick to pipe walls under debris and biofilms that problems can occur.
If a problem is found after corrosion has taken hold, flushing (forcing large volumes of water and chemicals through the pipework) is often used to clean out the system. Too much flushing can cause pipe to degrade and in itself introduces aerated water. It is therefore imperative that corrosive conditions are identified before damage occurs.
Real-time monitoring offers far better corrosion prevention for closed circuit systems, by continually tracking a range of parameters that can signify corrosive conditions - including dissolved oxygen. The 24/7 acquisition of key data effectively gives responsible parties the tools to stop corrosion before it even starts.
This approach can also reduce flushing requirements by minimising potential issues and tracking how quickly a system returns to safe levels – where sampling is the only means of checking closed-loop HVAC, there is a risk that flushing can be overused.
Click here to find out more about Hevasure and how it can improve the efficiency and reliability of your closed-loop HVAC system.