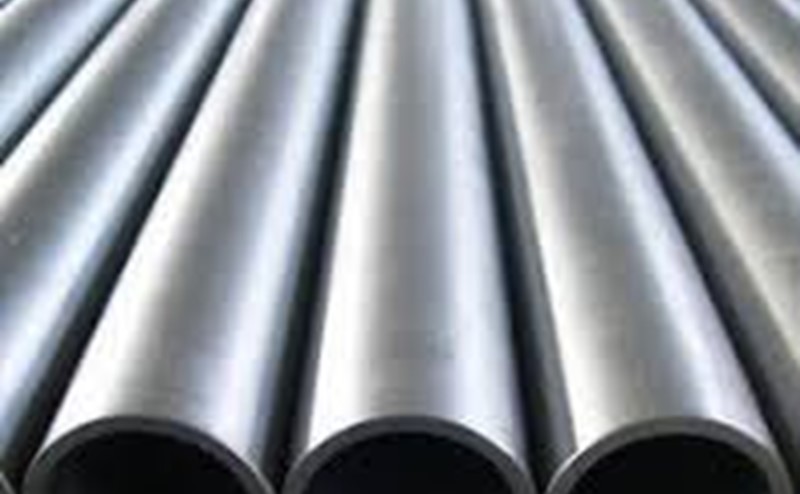
Thin-walled carbon steel, friend or foe?
Steve Munn, MD for Hevasure, discusses how to get the best from thin-walled carbon steel
Never has a simple piece of pipework stirred up such debate; from the haters who view it as flimsy and corrosion prone, to the lovers, extolling its cost-saving, eco-credentials and easy-to-install virtues; whatever your position, thin-walled carbon steel, specifically in a press-fit format, has been the subject of speculation for some time now.
I’m in the ‘lovers’ camp myself, but understand peoples’ frustrations – where it hasn’t been installed, commissioned and maintained correctly it is undeniable that problems can arise. Carbon steel press-fit is only suitable for closed-circuit systems where oxygen ingress is kept in check – let the O2 in and that’s where the issues begin.
Much has been talked about installation and how to prevent corrosion from the outset; proper storage that prevents dirt and damage, and of course correct fitting and pre-commissioning cleaning are key to getting the best out of this product.
Everyone accepts that pre-commission cleaning is vital to prolonging the life of steel pipework and this is covered extensively in BSRIA guide BG29:2012. What is sometimes not appreciated however, is that repeated cleaning with chemicals, can lead to more problems than they solve, especially in the case of thin-walled carbon steel.
Not only do chemicals strip away protective coatings but each subsequent flushing operation introduces a fresh load of aerated water. The oxygen either gets consumed in ‘flash rusting’ of the steel surface or hangs around to cause corrosion of other components such as brass fittings. So, ideally, closed water systems should be cleaned once (and only once), dosed with inhibitors and biocides and then left sealed and air-tight.
But, how can you be sure that problems don’t arise once the water system is up and running? Bad press surrounding thin-walled carbon steel may make many specifiers and end-users nervous of the product, sticking with fail-safe safe stainless steel, despite the fact that it will undoubtedly cost more overall.
The answer is real time monitoring. By having a true picture of water condition – from installation through to day-to-day operations – issues can be caught before corrosion begins. The Hevasure unit, for example, checks for a range of parameters including oxygen, inhibitor and corrosion levels, pH and pressure. Changes in these parameters are indicators of a problem which can then be investigated and hopefully dealt with, BEFORE more serious issues arise.
Sampling, the industry-standard for understanding water systems, is often a case of too little too late, with results taking weeks to come-back, analysis subject to human interpretation and oxygen not checked for.
So, there is a way to feel confident about using carbon steel, great! I know some of you will still be thinking ‘isn’t it just easier to use stainless steel? It’s corrosion resistant!’ While the pipework itself may be corrosion resistant, it isn’t stopping corrosion. Components used to fit the pipework together are commonly made from brass, copper, aluminium and mild steel which are not corrosion resistant and become the focus of degradation in systems piped with stainless steel. This is because, unlike in carbon steel systems, stainless steel does not scavenge out the oxygen introduced during the initial fill.
Whatever the pipe material used, it is always far better to prevent rather than mask corrosion; an approach which will also potentially reduce over-flushing and excess chemical usage.
If you want to make carbon steel your friend, saving large sums on material and installation costs, then monitoring is key to this relationship.