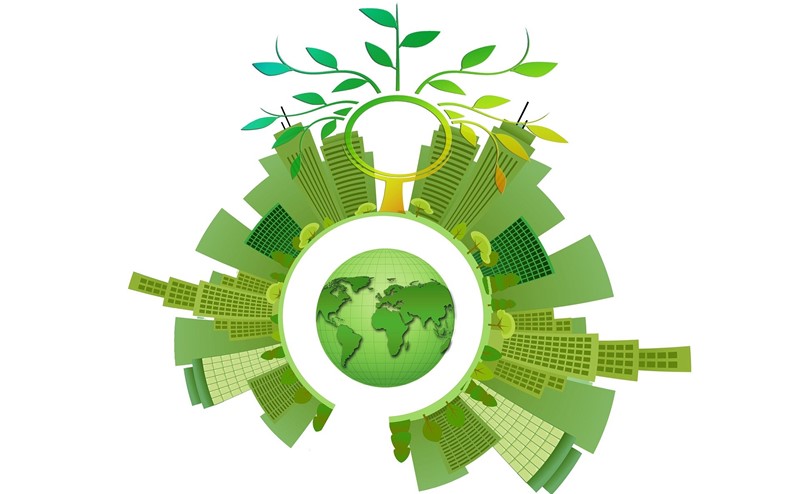
Improving HVAC sustainability through monitoring
Modern construction and building management has a focus on sustainability as we try to drive down the carbon footprint of our buildings – particularly of the large commercial variety. As voracious users of energy and water, improving the way HVAC systems operate is a key step in this process. Choosing the latest green technologies is of course important, but if these don’t function at their optimum and meet their design life, then some of the benefits are lost.
Closed circuit water systems are an essential part of almost all HVAC systems, and their efficient operation is therefore key to improving sustainability and preventing downtime. Commonly victimised by corrosion – an issue that leads to system fouling, pipe degradation, lack of efficiencies and breakdown – taking steps to keep corrosive conditions at bay is key to helping HVAC meet its potential.
Out with the old school
The ways of identifying corrosive conditions has, until the advent of Hevasure’s remote monitoring solutions, been decidedly old school. Sampling, laboratory analysis and corrosion coupons are a largely ‘stab in the dark’ approach when you compare the real-time data presented by our 24/7 technology.
Not only does this more traditional approach leave closed circuit systems more open to corrosion, it is also more likely that wasting processes, such as flushing and dosing may be employed. Flushing, used during precommission cleaning and sometimes after maintenance or where a bacterial problem has been identified, uses huge volumes of water. Flushing is a necessary evil, but if a better understanding of the true make-up of water condition is achieved, then sometimes it can be avoided.
For example, with Hevasure, you can monitor a period of maintenance, which will undoubtedly lead to disruption, such as the ingress of oxygen. If, however, things get back to ‘normal’ quickly, there’s no need to flush. Without Hevasure, a sample would be taken after the maintenance, likely to show adverse conditions. By the time the sample returns the water condition may have improved, but there is no way of knowing this, so flushing is used as a precautionary measure.
Hevasure can demonstrate the real-time corrosion rate of pipework and components, which, combined with an understanding of cumulative data provides a far better insight into what’s really going on, further reducing the impulse for knee-jerk reactions to ‘normal’ fluctuations in monitored parameters.
Flushing and the chemicals used for dosing also degrade pipework, so can actually exacerbate the shortening of a HVAC systems life.
On-going efficiency
Apart from not being real-time, the information sampling provides is not always that helpful.
Focusing on the constituents of the water (bacteria and chemicals) which while indicative of system health, frequently miss important indicators of system wide problems. In particular, the presence of corrosion debris such as iron or copper oxides can be under reported if they are insoluble or adhere to the walls of pipes and other components. High levels of bacteria (e.g. SRBs and pseudomonas) on the other hand may not be a problem if they are planktonic and not forming colonies under debris or biofilms. All this leads to false positives or negatives.
Crucially, sampling does not successfully identify dissolved oxygen, which is the root cause of almost all forms of corrosion, either directly (oxygen induced corrosion) or indirectly by creating the right conditions for bacteria to grow (microbial influenced corrosion).
Not only will a truer picture of a water systems lead to more efficient and long lasting HVAC systems, it may also facilitate better and more fit for purpose maintenance, which can result in leaner practices. Engineers are alerted to issues that need attention before damage occurs, rather than having to continually visit sites to check on key measures.
From reducing water wastage, to helping HVAC systems meet their design life and efficiency claims, real-time monitoring is a key step in sustainability. And, over the course of a systems life money will be saved – by preventing repairs, breakdown and downtime and also through reduced sampling, consultant and maintenance requirements.